The Flotation
Process
Until the
invention of the flotation process, the extraction of metal depended
upon being able to hand-pick the material in order to be economical.
Taking copper as an example, previously, that meant that using
low-grade ores - with less than four percent metal content - would not
be practical. In the present, however, available ores are typically
even lower in metal content. The current product from mines may
typically yield at best 2 percent to as low as 0.8 percent of the
metal, as fine particles of the mineral thinly distributed throughout
the rock. One hundred tons of ore contains 99 percent waste material
that must be separated to produce one ton of copper.
The flotation
process depends on the properties of minerals by which their surfaces
differ in the degree by which their surfaces can be wetted, and takes best advantage
of such
differences by suitable choice of the solution.
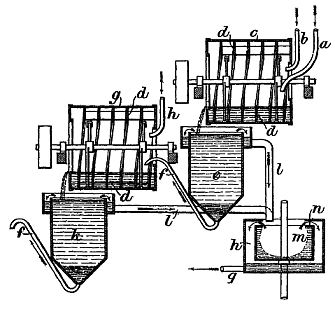
Illustration of an early flotation process
from the 1898 British Patent No.21948 by the Elmore brothers
Ore is first
ground into a powder, which is introduced to a series of tanks (known
as flotation cells) holding a solution containing oils, constantly
agitated, through which air is pumped. In the resulting froth. The
particles of copper minerals adhere to the raft of air bubbles on the
surface, while the majority of the worthless rock (known as the
gangue) sinks. The valuable material is skimmed from the surface froth;
the waste material is removed from the bottom of the tank.
With careful
control of the chemical conditions in such flotation cells, the results
can be selective for the desired product.
The huge amount
of material that must be handled for a relatively small yield requires
huge plants, fed continuously, operated by large companies able
to make the huge capital investment involved.
See also:
Flotation Process Patent
1898 by Alexander and Francis Elmore
Sixty
Centuries of Copper
(source)